Anisotropic Conductive Adhesive Bonding
On this page you will find more information about ACF Laminating and ACF Bonding. You will also find more information on how to choose the right ACF machine for your business manufacturing processes.
Electrical conductive adhesive bonds can be made between flexible and rigid circuit boards, glass panel displays and flex foils. In the process the adhesive will be heated and cooled under pressure by means of a thermode (hot bar). Conductive adhesive can be obtained in the form of foil, flex or paste. This adhesive contains small conductive particles or spheres. These are separated by an isolating matrix of adhesive material.
Anisotropic Conductive Film
Anisotropic Conductive Film (ACF), is a lead-free and environmentally-friendly interconnect system to make electrical and mechanical connections between two components. ACFs are widely used to perform flex-to-board or flex-to-flex connections used in LCDs. But also used for handheld electronic devices such as mobile phones, smart watches, or in the assembly of CMOS camera modules.
ACF Laminating / Pre-Bonding
The ACF material is supplied as a reel and consists of adhesive filled with conductive particles and a protective layer. Prior to laminating (or pre-bonding) the ACF to the substrate, the ACF tape is pre-cut at the required length from the ACF reel. Cutting is done using the half-cut method where only the actual ACF material is cut, the cover-layer is used for tape transport. The ACF is now positioned over the bond surface, by placing the thermode (hot bar) on the ACF material, the material is transferred to the substrate.
Heat Seal Bonding / ACF Final Bonding
Once the Pre-Bonding process is completed the two parts to be joined are brought together in a fixture. This fixture (or jig) makes sure that the bonding parts fit perfectly together and ensured the repeatability of the process. Here flex or other parts can be aligned with great accuracy to match the traces on the substrate or other parts that need bonding. Now more temperature, time and pressure are applied and cause plastic deformation of the adhesive and compression of the particles. The particles that are trapped between the conductors form a conductive interface between the pads on the two mating surfaces and conduct only in the Z axis. Subsequent cooling and full curing of the adhesive while still in the compressed condition stabilize the joint.
Benefits ACF Bonding / Heat Seal Bonding
- Lead-free process
- Smallest pitch >30 micron possible
- Flux free process
- Electrical connections to glass substrates
- No cleaning required after process
- Low process temperatures
ACF Bonding Features
- Precision Bonding: Achieve microscopically precise connections, ensuring optimal performance of electronic components.
- Enhanced Durability: With robust adhesive bonds, enjoy increased resistance to environmental factors, mechanical stress, and temperature variations.
- Versatility: Seamlessly bond diverse materials and substrates, including flexible rigid circuit boards, glass panel displays, and flex foils.
- Efficiency: Streamline your assembly process with fast and reliable bonding, reducing production time and costs.
ACF Laminating: Enhancing Electronic Assembly with Precision Bonding
ACF Laminating products are at the forefront of electronic assembly, offering unmatched precision and reliability in bonding various substrates. Typical applications of ACF Laminating include bonding flexible rigid circuit boards, glass panel displays, and flex foils with exceptional accuracy and durability. These products find extensive use in industries such as consumer electronics, automotive, aerospace, and telecommunications, where reliability and performance are paramount. From intricate smartphone displays to robust automotive instrumentation, ACF Laminating solutions cater to a wide range of applications, ensuring superior electrical conductive adhesive bonds that withstand the rigors of diverse environments. Whether it’s improving the structural integrity of flexible circuits or enhancing the functionality of display panels, ACF Laminating products deliver unparalleled results, driving innovation in electronic assembly processes.
ACF Laminating Process
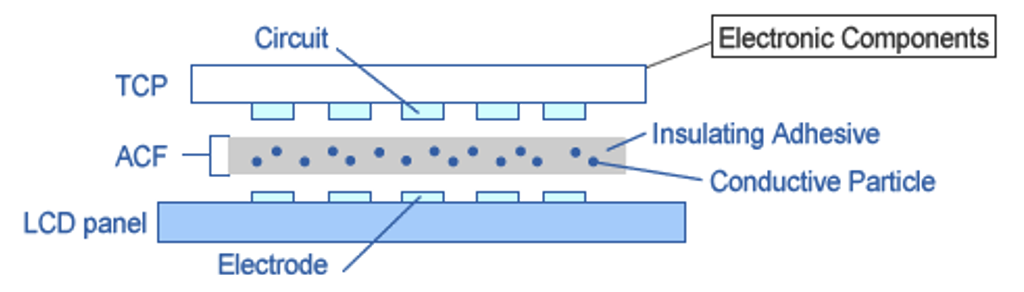
Choosing the right ACF Laminating Machine
Choosing the right ACF (Anisotropic Conductive Film) Laminating machine is crucial to ensuring the success and efficiency of your electronic assembly process. Here are some key factors to consider:
Application Requirements: Assess your specific bonding needs. Consider the types of materials you’ll be working with (e.g., flexible rigid circuit boards, glass panel displays, flex foils) and the desired bonding precision and durability.
Machine Capabilities: Look for machines that offer the necessary features to meet your application requirements. This includes factors such as bonding area size, temperature control, pressure regulation, and compatibility with different substrates.
Bonding Method: ACF Laminating machines utilize various bonding methods, such as heat and pressure application. Determine which bonding method aligns best with your application needs and production volume.
Precision and Accuracy: Ensure that the machine provides the level of precision and accuracy required for your specific bonding applications. Look for features such as micro-adjustable settings and advanced control systems to achieve consistent and reliable bonding results.
Ease of Use and Maintenance: Consider the user-friendliness of the machine and the availability of technical support and training. Opt for machines that are easy to operate, maintain, and troubleshoot to minimize downtime and maximize productivity.
Quality and Reliability: Invest in a machine from a reputable manufacturer known for producing high-quality and reliable equipment. Look for certifications, customer reviews, and warranties to assess the machine’s quality and reliability.
Scalability and Future Needs: Anticipate future growth and evolving application requirements. Choose a machine that offers scalability and flexibility to accommodate future upgrades or changes in production needs.
Cost Considerations: Evaluate the upfront cost of the machine along with long-term operating costs, including energy consumption, maintenance, and consumables. Balance cost considerations with the machine’s capabilities and performance to ensure a cost-effective investment.
Choosing the right ACF Laminating machine carefully
By carefully considering these factors and conducting thorough research, you can choose the right ACF Laminating machine that best suits your application requirements, budget, and long-term goals. Additionally, consulting with industry experts and manufacturers can provide valuable insights and guidance in the decision-making process.
C-Tack
The C-Tack Desktop System developed by C-Tech Systems for ACF Laminating (Pre-Tacking) applications.
C-Turn ACF
C-Turn handles the product in a pneumatic turning unit for easy access and preparation of the application.
Process calibration tools
For all Hot bar application, Process Calibration instruments are imperative to ensure and maintain a reliable, repetitive and accurate production processes. C-Tech Systems offers calibration tools for planarity, temperature and pressure calibration. All created to meet the parameters and manage the processes precisely.
Get in touch with us today!
Ready to elevate your precision bonding production process? Explore our range of hot bar soldering machines and discover the potential for precise, reliable solder connections in your electronics manufacturing processes. Do you have questions regarding our ACF Laminating technology? Don’t hesitate to contact us today.