C-TECH SYSTEMS
C-Tack
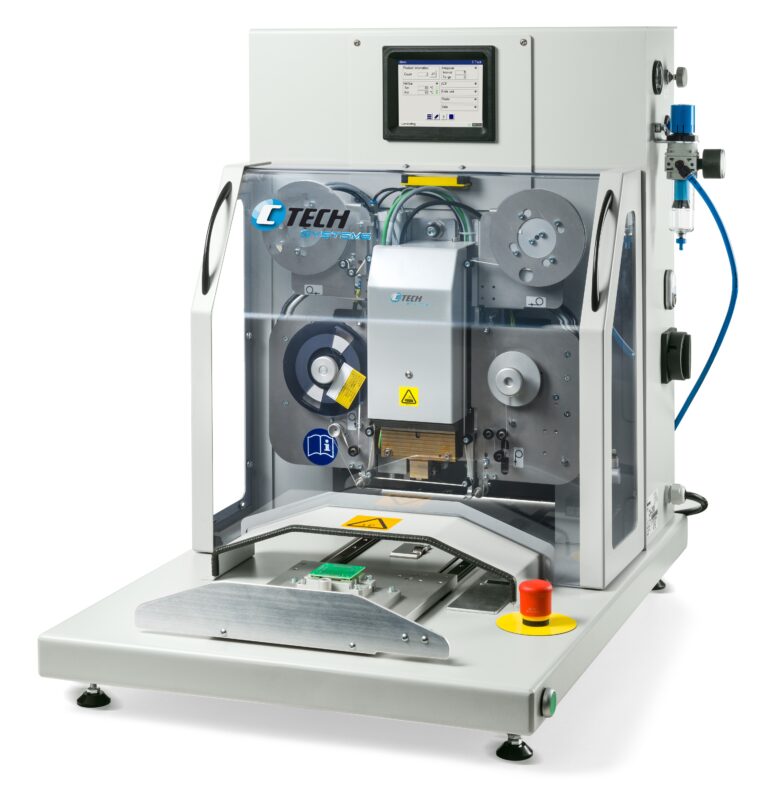
For ACF Laminating (pre-tacking) applications
The C-Tack Desktop System developed by C-Tech Systems for ACF Laminating (Pre-Tacking) applications. It uses pneumatic bonding head technology and offers reliable process control, with an integrated Constant Heat power supply. ACF (Anisotropic Conductive Film) Laminating is a Hot Bar bonding technique to make electrical bonds between flexible and rigid circuit boards, glass panel displays and flex foils. ACFs are widely used to perform LCD-to-flex, flex-to-board or flex-to-flex connections. The ACF Laminating/Pre-Tacking process forms the first part of the total bonding process: applying the adhesive material to the substrate. After that the final Heat Seal Bonding process can take place.
Before the ACF is applied to the substrate, the ACF tape is half-cut at the required length from a reel of ACF. Half-cut means that only the actual ACF material is cut, not the cover layer, which is used for tape transport. By use of a customized thermode with Constant Heat technology (Hot Bar) the ACF is applied to the bond surface. The integrated control system monitors and regulates the temperature, process time and force applied for the pre-tacking process. All process parameters are embedded into the system ensuring consistent process quality and operator independence.
The product parts are positioned in a customized product fixture, which is mounted to the pneumatic linear slide (front-rear stroke). The C-Tack system enables full automatic process control, with manually loading and unloading of parts.
The C-Tack is standard compatible with almost all ACF tape available in the market.
ACF Laminating / Pre-Tacking
Electrical conductive adhesive bonds can be made between flexible and rigid circuit boards, glass panel displays and flex foils. Conductive adhesive contains small conductive particles, which are separated by an isolating adhesive material. Anisotropic Conductive Film (ACF), is a lead-free and environmentally friendly interconnect material to make electrical and mechanical connections between two parts. ACFs are widely used to perform LCD-to-flex, flex-to-board or flex-to-flex connections.
Prior to laminating the ACF to the substrate, the ACF tape is pre-cut at the required length from a reel of ACF. The tape is half-cut; only the actual ACF material is cut. The cover layer (carrier) is used for tape transport. The ACF can now be applied to the substrate by using the Constant Heat Thermode (Hot Bar). Time and temperature can be programmed, force can be adjusted.
After the pre-bond is made the peeler shifts from right to left and back again, to peel the ACF tape from the carrier tape. The ACF is has now been pre-bonded to the surface. Now the laminating process is finished, the slide comes out again. The C-Tack system is now ready to receive the next substrate.
Next process: Heat Seal Bonding
After laminating, the parts to be joined are brought together in a fixture. This fixture (or jig) makes certain that the bonding parts fit perfectly together and ensures the repeatability of the process. Temperature, time and pressure are applied and cause plastic deformation of the adhesive and compression of the particles. The particles trapped between the conductors form a conductive interface between the pads on the two mating surfaces and conduct only in the Z-axis. Subsequent cooling and full curing of the adhesive while still in the compressed condition stabilize the joint.
-
De Boelakkers 4, 5591 RA, Heeze
The Netherlands - info@c-techsystems.com
- +31 (0)6 - 28 92 4037
- https://www.c-techsystems.com
-
Mon to Sat - 9:00am to 6:00pm